Wheel Blast Systems
Wheel blasting has used for almost every type of application there is in metal finishing. Below are the most popular applications/industries where this process has been used.
Automotive parts, automotive reman parts, foundries, aluminum die castings, scale and rust removal, deburring, surface prepping, pipe cleaning, custom steel fabrications, aerospace, metal fabricators, paint removal, peening of springs and aerospace components, and deflashing metal and plastic profiles.
Spinner Hanger Systems
Spinner Hangers provide an ideal solution for batch blasting of many types of parts too fragile or awkward for other methods to clean. These systems clean efficiently for high speed productions. Our systems include two work chambers mounted on an indexing turntable. As the turntable steps through programmed positions, one chamber exposes parts to a contained blast stream from high-efficiency wheels while the other opens to the operator. Parts are then unloaded and reloaded into the chamber for the next cylce . To assure uniform coverage, a spindle rotates the hangers within the working chamber’s blast envelope. PLC programming assures repeatable performance cycle after cycle, and cast liners on work-chamber walls extend equipment life. Hanger capacities from 125 to 2,000 pounds fit most applications.
- Speed batch blasting of sensitive parts
- Deliver 360° work piece coverage
- Continue working during loading
- Multiple indexing
- PLC programmed
- Safety bump bar strip
Tumble Blasters
Tumble Blasters process multiple parts, ranging in size from small to medium, with a level of speed and efficiency unmatched by other types of equipment in a comparable price range. Tumble Blasters come in ten standard models with load capacities ranging up to 3,000 pounds or 24 cubic feet. Smaller units are available with either wheel or air-blast systems to handle a broad spectrum of media. We offer tumble blasters for small footprint cell stations. These rugged machines automate cleaning, peening, deburring, profiling, finishing and many other surface-conditioning tasks on a vast range of parts.
Traditional Industries and Applications for this Product
Wheel blasting has used for almost every type of application there is in metal finishing. Below are the most popular applications/ industries where this process has been used.
Automotive parts, automotive reman parts, foundries, aluminum die castings, scale and rust removal, deburring, surface prepping, pipe cleaning, custom steel fabrications, aerospace, metal fabricators, paint removal, peening of springs and aerospace components, and deflashing metal and plastic profiles.
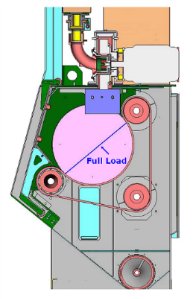
Pass Through Wire Mesh Belt System
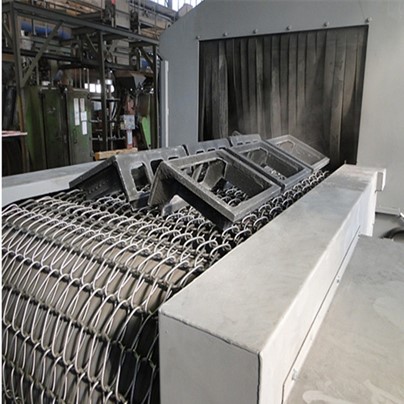
This design is for continuous high production cleaning of parts and castings. Parts placed on the wire mesh belt conveyor continuously pass through the vestibule into the blast chamber. The number of blast wheels coupled with the blast wheel horsepower determine the cleaning capacity and production capabilities of the machine.
Features of the Wire Mesh
- Manganese wire mesh conveyor belt
- Variable speed conveyor belt
- Quantity of blast wheels from 2 to 12
- Direct drive blast wheels
- Automatic (pneumatic) belt tensioning system
- Standard and custom designs
Table Blast Systems
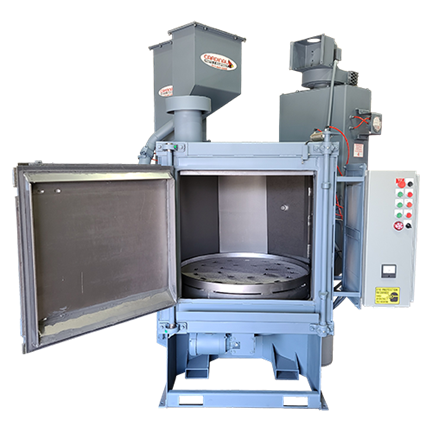
These rugged machines facilitate cleaning, peening, deburring, profiling, finishing and other surface conditioning tasks in metal-intensive industries involving casting, welding and fabrication. Parts are loaded onto a powered turntable which rotates within the blast envelope to provide 360° exposure to the blast stream. Models with an oscillating blast wheel, such as our 36″ Power Table, enhance blast coverage. Features like the swing door on our Table Blasters expedite loading and unloading by enabling the operator to swing the system’s door-mounted turntable in and out of the blast enclosure.
All models feature abrasion-resistant liners on turntables for extended service life. Models used with heavy parts are designed for overhead loading and unloading with either a hoist or crane.
- Versatile, rugged systems that deliver consistent, repeatable results
- Easy to install, simple to operate
Cardinal Table Blasters process parts weighing up to 10,000 pounds with diameters up to eight feet and heights exceeding four feet. Featuring eleven standard models, Cardinal line of Table Blasters provides the versatility and flexibility to efficiently blast parts ranging from ten-pound gears to heavy fabrications.
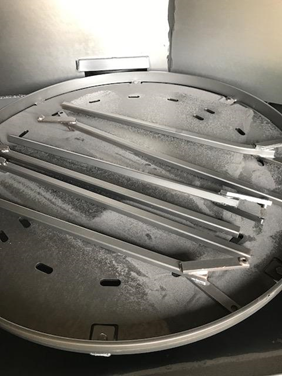
