The widest choices of Wet Blast, Abrasive Wet Blasting, Vapor Honing, Vapor Blasting, and Abrasive Blasting Finishing Equipment!
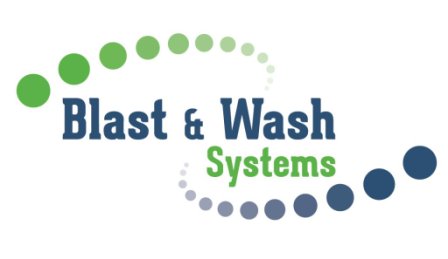
Choose Your Wet Blast System:
Vapor honing or wet blasting involves combining water & abrasive together to form a slurry which is propelled at the part surface using compressed air. Abrasive selection is made based on desired surface roughness or aesthetical finish. Unlike dry blasting, you can mix abrasives together to give you the finish you want to achieve!
Scroll below to view our wide selection of wet blast cabinets. Whether you need to blast small delicate parts or large vessels, we have systems to get the job done. We offer units for the hobbyist, small shop to rugged industrial cabinets. For portable abrasive wet blasting we offer 4 models for outdoor use. Call us at (585) 384-9025 for any questions.
Hobbyist / Small Shop Models:
- Right hand side load door.
- Built from rugged polymer our hobbyist model is built to last.
- Lifetime warranty best in the industry. Rest assured your investment is covered.
Full Range Service: Cycle, Powersports, and Engine Specialists
- 33″W x 30″D x 28″H inside workspace
- Total Vapor Hone foot print 36″W x 35″D x 5′ 8″H
- Single Piece HDPE Plastic Construction 1/4″ thick walls
- 110V Single Phase Power Supply
*Available open loop or closed loop system.
VH 900 Front Load Specs:
- Workspace – 36″W x 24″D x 30″H (small enough to fit through doors)
- Power – 110V Single Phase of 220V
- Abrasive Amount – 34 lbs.
- Water Amount – 24 Gallons
- Pump – High Volume Slurry Pump
- Pump Impeller – Industrial Polyurethane Pump Impeller
- Nozzle – Standard Manual Rinse Nozzle
- CFM – 20-30 CFM
- PSI – 80-90 PSI
- Closed Loop System
- Stainless Steel
- Precision Regulator
- (2) 2′ LED Light Bar
- 1/2 NTP Air Connection
- Casters Included
- Window Wipers Included
- No Assembly Required (fully factory tested and assembled before shipping)
VH 900 w/Tumble Basket Specs:
- Stainless steel
- Precision Regulator
- VH900 is a closed loop system
- 2 LED light bar for better visibility
- 1/2 NTP air connection
- Front load door, very convenient
- Small enough to fit through doors
- Comes with casters
- High flow pump
- Manual rinse nozzle is standard
- Window wipers for better visibility
- Fully factory tested and assembled before shipping
VH 6030 Closed Loop Stainless Steel
Econ VH6030 Specs:
- Workspace: 60W x 30D x 38H
- Footprint: 60W x 38D x 84H
- Open / Closed Loop Option
- Standard Regulator
- (2) 2′ LED Light Bar
- (2) Wipers Included
- Window Rinse and Internal Rinse Nozzle Included
- Foot Pedal Control
- 110v Only
- Requires: 25 CFM @ 60-100 PSI
The Aqua Wheelblaster uses wet blasting technology to finish and provide a key for alloy wheels, specifically after curb repairs. The process uses an abrasive mixed with water into slurry to blast off the alloy and provide an ideal surface for the paint and/or lacquer to adhere to in the next stage of the restoration process.
The machine combines the standard six-stage process of manually preparing wheels into one application. It can reduce the application time from one hour per wheel to less than 5 minutes in one compact cabinet.
The machine combines the standard six-stage process of manually preparing wheels into one application. It can reduce the application time from one hour per wheel to less than 5 minutes in one compact cabinet.
Industrial Cabinet Systems:
- Right hand side load door.
- Optional track and car available.
- Industrial machine built to last a lifetime.
- Lifetime warranty best in the industry. Rest assured your investment is covered.
Vapor Hone 2000
- 40″W x 40″D x 40″H inside workspace
- Durable 12ga Steel construction
- 2 Waterproof LED lights for better workspace visibility.
- Safety Door Interlock Switch
- GFCI Protection Hardwired into main power line
- High Volume Polyurethane Pump
- Pump agitation for greater slurry mixing and cleaning effect
- Production Blast Gun with boron carbide insert
- 60-100psi @ 20- 30 CFM
- 25 gallons of water and 20lbs of abrasive media needed to charge machine
- Rated 100% duty cycle
- 2yr warranty on submersible slurry pump system
- Foot switch operated blasting gun for easy process control
- Minimum 5hp compressor recommended capable of 20-30 CFM or greater
- 60″W x 30″D x 38″H inside work space.
- Total machine foot print 75″W x 38″D x 7’H
- Durable Stainless Steel 12ga construction
- 110v Single Phase Power
- 60″W x 48″D x 38″H inside work space.
- Total Vapor Hone foot print 60″W x 50″D x 7’H
- Durable Stainless Steel 12ga construction
- 110v Single Phase Power
Vixen Aquablast 915 – SS housing
Dimensions 36”W x 29.5”D x 34” H
Vixen Aquablast 1215 – SS housing
Dimensions 47.75”W x 41.25”D x 34” H
Vixen Aquablast 1515 – Dual workstations – SS housing
Dimensions 59”W x 53”D x 40.25” H
Vapor Honing Heavy Duty VH1000 Closed Loop Wet Blast System
Standard Features:
- 36″W x 30″D x 38″H inside work space
- Total machine foot print 40″W x 40″D x 84” H
- Durable 12ga Stainless Steel construction
- 220V/ 3phase
- 2 – 2ft LED waterproof lights for excellent visibility
- Precision Regulator
- Window wiper system
- Safety Door Interlock Switch
- High Volume Polyurethane Pump
- Pump agitation for greater slurry mixing and cleaning effect
- Production Blast Gun with boron carbide insert
- 30 CFM required
- 30 gallons of water and 20lbs of abrasive media needed to charge machine
- Industrial Filtration CL System
- 2yr warranty on submersible slurry pump system
Optional Features:
- Two stage cartridge filtration system ( 5 micron)
- Immersion Heater
- Abrasive Density Meter
- Rubber Lined Walls for Abrasion Resistance
- Track and Car System for Loading Heavy Parts
- 26” 1000 lb capacity stainless steel turntable (this is included with track & car system)
- 460V 3 phase
Vapor Hone 2000
- 40″W x 40″D x 40″H inside workspace
- Durable 12ga Steel construction
- 2 Waterproof LED lights for better workspace visibility.
- Safety Door Interlock Switch
- GFCI Protection Hardwired into main power line
- High Volume Polyurethane Pump
- Pump agitation for greater slurry mixing and cleaning effect
- Production Blast Gun with boron carbide insert
- 60-100psi @ 20- 30 CFM
- 25 gallons of water and 20lbs of abrasive media needed to charge machine
- Rated 100% duty cycle
- 2yr warranty on submersible slurry pump system
- Foot switch operated blasting gun for easy process control
- Minimum 5hp compressor recommended capable of 20-30 CFM or greater
High Pressure Parts Washer Blast (No Abrasive):
The Aqua Wheelblaster uses wet blasting technology to finish and provide a key for alloy wheels, specifically after curb repairs. The process uses an abrasive mixed with water into slurry to blast off the alloy and provide an ideal surface for the paint and/or lacquer to adhere to in the next stage of the restoration process.
The machine combines the standard six-stage process of manually preparing wheels into one application. It can reduce the application time from one hour per wheel to less than 5 minutes in one compact cabinet.
The machine combines the standard six-stage process of manually preparing wheels into one application. It can reduce the application time from one hour per wheel to less than 5 minutes in one compact cabinet.
Features:
- Full stainless steel construction
- Quick release highly efficient submersible polyurethane pump
- PLC controller for the following:
- -Blast cycle times
- -Rinse cycle times
- -Water temperatures
- -Drain valve opening & closing
- -Windscreen wiper & rinser
Optional Extras:
- 1 or 2 stage rinse
- Unload facilities
- Additional blast guns
- Hot rinse
- Demineralized rinse
- Cycle indicator
- Touch screen controls
Wet Blast Automation:
Vapor Honing Automated Gladiator
All in one – Wet blast, Wash, & Rinse
Now you can Vapor Hone your parts automatically in this versatile system by placing parts on the powdered turntable – fully programmable! Inset a fixture on the turntable and you can hang multiple parts for 360-degree coverage. Blast clean multiple parts in just one cycle! Even use your choice of abrasive!
After wet blast cleaning, you can rinse and dry the parts in the same cabinet. Spray parts with soap during a heated wash, rinse with recirculating water, and blow dry parts.
Specifications:
Workspace: 36”W x 30”D x 30”H
Footprint: 64”W x 58”D x 83”H
- 220V 3phase
- 4 Blast guns
- 7 rinse nozzles
- 30CFM needed
- 100 – 120PSi
Available options:
- Filtration
- Temperature controls
- Program blast height adjust feature
- HMI interface
- Your choice of abrasive
- Heated wash – spray parts with soap
- Rinse – spray parts with recirculating water
- Blow dry and more!
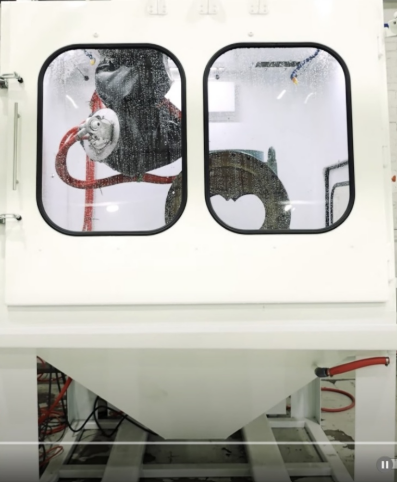
What sets the Robo-IQ apart is its in-house programmability. Whether introducing new parts or adapting to design changes, your team can quickly reprogram the system, allowing you to stay agile and in control without relying on external services.
Measuring in at 36″ the Robo-IQ’s turntable is large enough to handle multiple smaller parts in an indexing configuration, or one large part. We do not recommend the part to be taller than 30″ or heavier than 2,000 pounds.
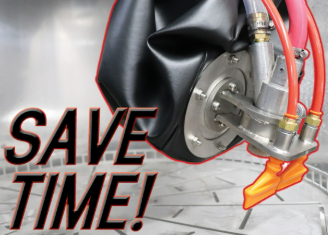
VHT Robo-IQ Robotic Wet Blaster
- Main access door: 54″W x 43″H
- Side access hatch: 36″W x 22″H
- 30 CFM at 60-100 PSI
- 220V Single Phase Power
- Holds 60 Gallons of Water
The Robo-IQ is designed to handle a diverse range of parts, it’s programmable in-house and incredibly cost-effective. Whether you are processing small CNC-machined components, large engine blocks, or aircraft turbine blades, and more, the Robo-IQ is the perfect choice.
The Robo-IQ is engineered for versatility, making it perfect for a wide range of applications. With simple waypoint programming, large and complex parts are easily handled, ensuring precise treatment. For smaller parts, multiple components can be fixtured and processed in batches using an index-style program, maximizing efficiency.
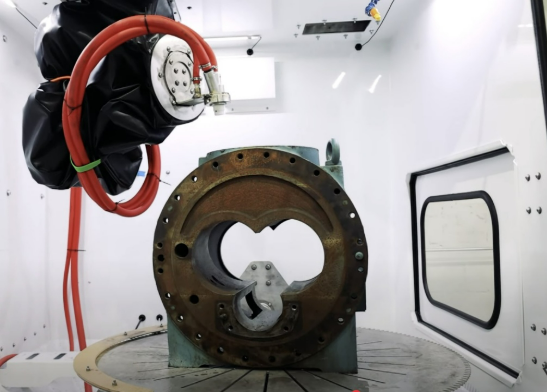
Blast & Wash Systems offers a wide selection of abrasive wet blasting equipment, including vapor before-wet-blast honing, wet abrasive systems, wet sandblast cabinets, wet abrasive equipment, wet blast tabletop units and vapor blasting systems.
Wet blasting is used for blasting aerospace components, smoothing 3D printed parts, titanium medical fasteners, aluminum wheels, impellers, engine blocks and other car parts, motorcycle parts, valves, plastic deflashing and more!
The finishes you can achieve are endless! Choose an abrasive and add it into the system to deburr, descale, deflash, remove layers of paint, blend machine lines, degrease and clean. No DUST!