Giant Finishing, Inc.
Giant Finishing has equipment and other vibratory deburring machines for all your surface finishing needs.
Combine our mass finishing equipment with the right deburring media, vibratory deburring chemical compounds, with the right time cycle and settings to get the correct finishing process. Giant can help increase your production, finish your parts more consistently.
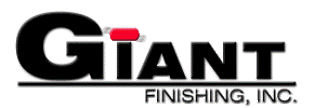
Surface finishing may require special processes with specialized deburring compounds including liquid or dry chemicals.
Giant Finishing is your one stop shop for vibratory deburring equipment, tumbling bowls, tubs or ovals, metal finishing equipment, abrasive tumbling media, & finishing compounds. Plastic media, ceramic media, steel vibratory media we have it all.
The mass finishing industry is what we work with every day at Giant Finishing. We build most finishing equipment on a custom level and we strive to meet each customers unique needs. We can fabricate machines to fulfill your ideas, if you have a specific request, ask us about it and we can take care of any questions you may have.
Along with our competitive prices, we offer a variety of choices that assist in the vibratory deburring options with different media and chemical compound selections. We can provide you with the right solution to finish your parts.
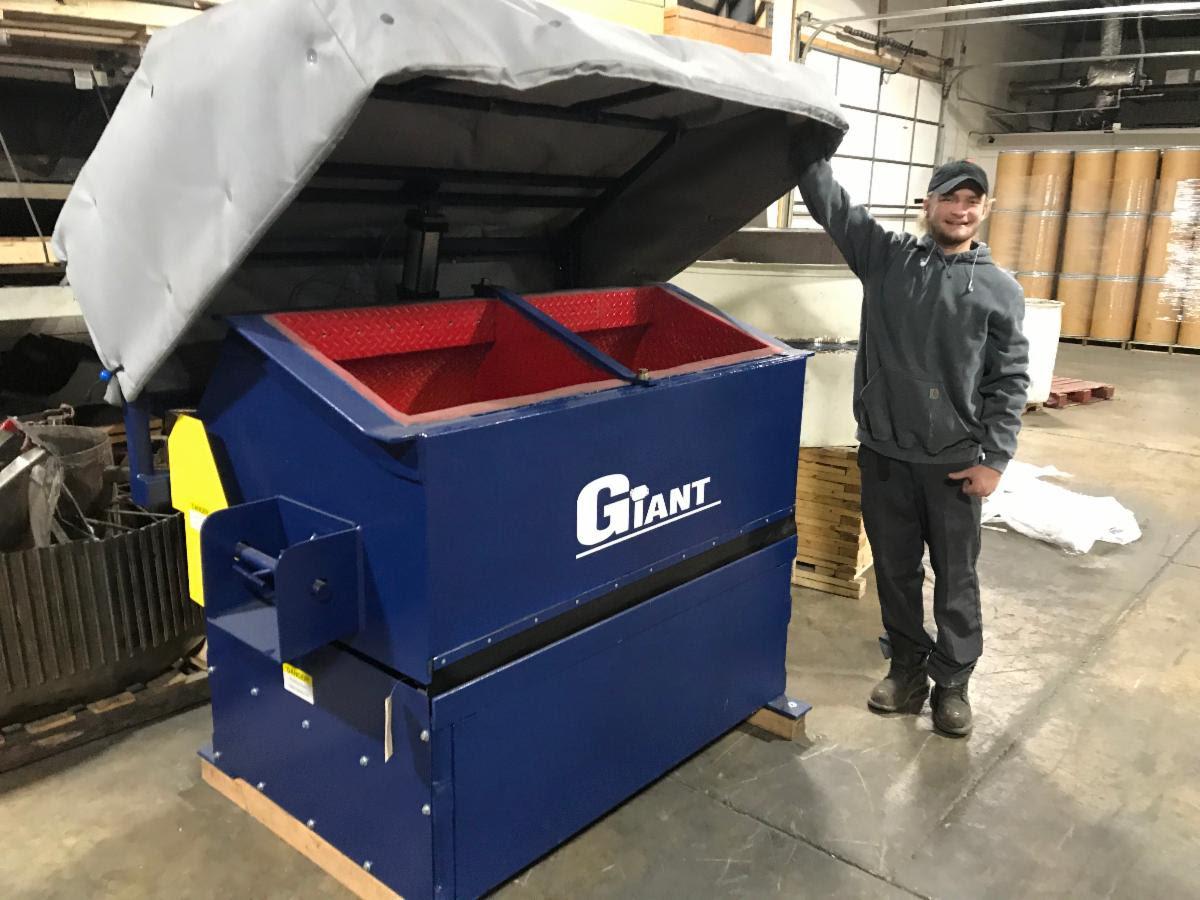